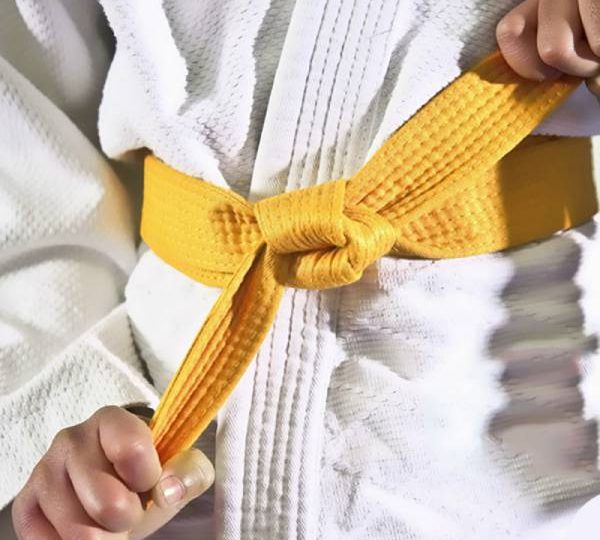
Yellow Belt Lean Six Sigma: An Essential Tool for Business Improvement
Understanding Yellow Belt Lean Six Sigma
Yellow Belt Lean Six Sigma serves as an essential starting point for those interested in process improvement. It equips individuals with fundamental knowledge about Lean Six Sigma principles. Furthermore, this certification enables participants to identify inefficiencies within workflows. By learning effective tools and methods, Yellow Belts contribute significantly to quality management. They also develop skills that help them engage with more experienced practitioners. This collaborative environment fosters improved outcomes and encourages a culture of continuous improvement.
The Role of Yellow Belts in Organizations
Yellow Belts play a crucial role in supporting green and black belt professionals. They help with data collection and project implementation tasks. This involvement is critical because it ensures that projects progress smoothly and efficiently. Moreover, Yellow Belts can share their insights, which enhances team discussions. Their fresh perspectives might uncover solutions that senior professionals may overlook. Additionally, these individuals gain practical experience, which prepares them for higher-level certifications in Lean Six Sigma.
Ultimately, investing in Yellow Belt training boosts overall organizational effectiveness. Companies reap the benefits of having a skilled labor force capable of improving processes. The synergy between Yellow, Green, and Black Beltscreates a strong foundation for success. Engaging every member in continual learning cultivates a proactive culture. Thus, Yellow Belt Lean Six Sigma serves as a gateway to more advanced practices. Overall, this certification fosters motivation and teamwork among employees. It paves the way for increased quality and efficiency in every aspect of the organization.
The Importance of Yellow Belt Lean Six Sigma Training
The Importance of Yellow Belt Training
Training in Yellow Belt Lean Six Sigma equips employees with essential skills for process improvement. This knowledge allows them to engage actively in projects that enhance efficiency. Additionally, they learn the DMAIC framework, which guides them through each stage of improvement. Employees can define problems clearly, measure performance accurately, analyze data effectively, improve processes systematically, and maintain control over changes. Consequently, this structured approach promotes a culture of continuous improvement within organizations.
Bridging the Gap to Higher Efficiency
By identifying waste, employees can enhance value across various processes. They gain insights into existing flaws and develop strategies to mitigate them. As teams apply their training, they often see significant improvements in workflow. This leads to higher efficiency levels, which benefits both the organization and its customers. When processes operate smoothly, customer satisfaction tends to increase.
Therefore, companies that invest in Yellow Belt training foster a proactive workforce. Employees take ownership of their roles and contribute to overall success. Ultimately, the collaboration between trained staff members boosts morale and drives innovation. In this way, Lean Six Sigma principles create a sustainable path toward operational excellence.
Key Concepts of Yellow Belt Lean Six Sigma
Understanding the basic concepts of Yellow Belt Lean Six Sigma is essential for anyone involved in process improvement. This methodology merges two critical approaches: Lean and Six Sigma. Lean focuses on eliminating waste and streamlining processes, which maximizes efficiency. On the other hand, Six Sigma aims to reduce variation, thereby improving overall quality. By combining these approaches, organizations can develop a comprehensive toolkit that drives operational excellence. Thus, employees at all levels should grasp these foundational elements to contribute effectively.
Applying the Methodology in Organizations
Applying Yellow Belt Lean Six Sigma effectively requires practical knowledge and skills. Organizations must train their teams in these concepts to ensure proper implementation. Employees can then identify areas for improvement within their processes. Moreover, they can utilize Lean strategies to eliminate unnecessary steps.
At the same time, they should integrate Six Sigma techniques to minimize errors and variations. This dual focus not only enhances productivity but also ensures a higher quality of output. Ultimately, organizations that adopt these principles will see improved performance and customer satisfaction. Thus, investing in Yellow Belt training reaps significant rewards for both the employees and the organization.
The Role of a Yellow Belt in Projects
Role of Yellow Belt Lean Six Sigma Holders
Individuals with a Yellow Belt Lean Six Sigma certification play a vital role in improvement projects. They serve as essential team members, supporting project leaders by providing critical data. This data helps the team understand current processes and identify areas for improvement. Additionally, Yellow Belt holders track progress throughout the project, ensuring that everything stays aligned with the overall objectives. They also maintain open lines of communication within the team, which fosters a collaborative atmosphere. The teamwork encourages every member to share ideas, leading to innovative solutions.
Impact on Improvement Initiatives
The involvement of Yellow Belt certified individuals significantly boosts process improvement initiatives. Their contributions ensure that all team members remain focused on common goals. When everyone works together, they can tackle challenges more effectively and efficiently. This collaborative spirit often generates enthusiasm, which motivates team members to excel.
Furthermore, Yellow Belt holders can help identify potential obstacles early, allowing the team to address them proactively. As a result, projects can move forward without unnecessary delays. Ultimately, the Yellow Belt certification empowers individuals to contribute meaningfully, enhancing the overall success of the project. Their skills in data gathering and communication not only benefit the team but also reinforce a culture of continuous improvement. By working together, Yellow Belt members help ensure the success of process improvement efforts across the organization.
Benefits of Yellow Belt Lean Six Sigma Certification
Benefits of Yellow Belt Certification
Obtaining a Yellow Belt Lean Six Sigma certification brings many advantages for individuals and organizations. First, this certification enhances problem-solving skills significantly. Individuals learn to analyze problems more effectively, leading to innovative solutions.
As they gain expertise, they also develop a deep understanding of key metrics and performance indicators. This knowledge proves essential for making informed decisions in their roles. Furthermore, the certification provides a structured approach to process improvement, allowing team members to contribute effectively. As practitioners advance to Red Belt Jiu Jitsu, they gain deep insights into performance metrics, enabling informed decisions and effective contributions to team strategies and process improvements.
Career Advancement Opportunities
In addition to skill enhancement, obtaining this certification can significantly boost career prospects. Employers often seek candidates who demonstrate a commitment to excellence and continuous improvement. A Yellow Belt certification showcases this commitment, making individuals stand out in a competitive job market. With this recognition, certified individuals can pursue higher positions or diverse roles within their organizations. Earning a Yellow Belt Certification not only enhances skills but also elevates career opportunities, making candidates more appealing to employers in a competitive job market.
They can also participate in projects aimed at optimizing processes, which may lead to career advancement. Therefore, investing time and effort into earning a Yellow Belt shines a spotlight on one’s dedication to growth. By embracing Lean Six Sigma principles, individuals not only enhance their capabilities but also positively impact their organizations. This approach fosters a culture of efficiency and effectiveness, benefiting everyone involved. In conclusion, obtaining a Yellow Belt Lean Six Sigma certification is a strategic choice for anyone looking to improve their skills and advance their careers.
Implementing Yellow Belt Lean Six Sigma in Organizations
Organizations can implement Yellow Belt Lean Six Sigma by creating structured training programs. Administering workshops is an effective way to educate staff about the methodology. Companies can also encourage employees to pursue certification by offering resources and time for study. By fostering a culture of continuous improvement, organizations can maximize the impact of their Yellow Belt Lean Six Sigma initiatives. To foster a culture of continuous improvement, organizations can also explore casual team-building activities, like wearing a Yellow Turtleneck Sweater Mens, to create a cohesive atmosphere.
Conclusion: Embracing Yellow Belt Lean Six Sigma for Future Success
In today’s competitive landscape, businesses must embrace methodologies like Yellow Belt Lean Six Sigma. This certification equips employees with essential tools for quality improvement and operational efficiency. As employees adopt these practices, they contribute to a culture of excellence. Therefore, organizations that invest in Yellow Belt Lean Six Sigma training will likely see significant benefits. By nurturing this skill set, companies can position themselves for long-term success.